PRODUCT PARAMETERS
Description
Introduction to Custom made plastic helical gear with metal shaft
Custom made plastic helical gear with metal shaft are important components in mechanical systems used to support rotating parts (such as gears, pulleys or sprockets) and transmit torque. They play a key role in mechanical equipment by connecting the power source with the working parts to ensure the effective transmission of power.
Characteristic advantages of Custom made plastic helical gear with metal shaft
High precision: adopting precision machining technology ensures the size and shape accuracy of the shaft and improves the transmission efficiency.
High strength: made of high-quality materials with good tensile, compressive and wear-resistant properties.
Reliability: After strict quality control, it ensures stable operation for a long time.
Versatile design: A variety of specifications and types are available to suit different applications.
Easy maintenance: the structure is designed for easy installation and repair, reducing maintenance costs.
(Custom made plastic helical gear with metal shaft)
Specification of Custom made plastic helical gear with metal shaft
Tailor-made plastic helical equipments with metal shafts are precision-engineered elements made for applications requiring smooth, silent, and reliable power transmission in varied markets. These gears integrate the light-weight, corrosion-resistant residential properties of high-performance plastics with the architectural toughness of metal shafts, providing a balanced remedy for modest to high-load situations. The helical equipment teeth are reduced at an angle (typically 15– 30 levels) to the axis, ensuring steady engagement for minimized sound, reduced vibration, and greater load-bearing capacity compared to stimulate gears. The plastic equipment is usually produced from products like nylon (PA6, PA66), POM (acetal), or PEEK, chosen for their wear resistance, low friction, and ability to operate in settings where lubrication is limited. The steel shaft, usually constructed from stainless-steel, carbon steel, or light weight aluminum, is incorporated right into the gear using press-fitting, sticky bonding, or insert molding to make sure a safe, backlash-free link. Personalization alternatives include gear component (0.5– 5+), number of teeth (10– 200+), pitch size (10– 500+ mm), face width, helix angle, and shaft dimensions (diameter, length, keyways, splines, or D-shaped ends). Running temperature levels range from -40 ° C to +120 ° C (as much as +250 ° C for PEEK ), with load abilities tailored to application requirements. Resistances comply with ISO or AGMA criteria (normally IT6– IT8 for shafts, DIN 3– 5 for gears). Surface area surfaces are optimized to minimize friction and wear. These gears are excellent for vehicle systems, clinical gadgets, commercial equipment, robotics, and consumer electronic devices. Benefits include minimized weight, rust resistance, sound dampening, and cost-effectiveness contrasted to all-metal options. Personalized orders require specs such as torque requirements, RPM, ecological problems (chemical exposure, dampness), and placing details. Prototyping and screening (e.g., tons endurance, thermal biking) guarantee performance recognition. Lead times differ based on intricacy, with minimal order amounts (MOQs) flexible for small sets. Compliance with ISO 9001, RoHS, or FDA criteria is available upon demand.
(Custom made plastic helical gear with metal shaft)
Applications of Custom made plastic helical gear with metal shaft
Tailor-made plastic helical equipments with metal shafts are specialized mechanical components designed to provide high efficiency, resilience, and performance sought after applications. These equipments incorporate the light-weight, corrosion-resistant residential properties of engineering plastics like POM, nylon, or PEEK with the architectural toughness of metal shafts (commonly stainless steel or aluminum). The helical style, with angled teeth, guarantees smoother interaction, lowered noise, and higher lots capacity compared to spur equipments. Below are essential applications where these elements succeed:
** Automotive Solutions **: Made use of in transmission systems, electrical power steering, and cooling and heating actuators, these equipments lower weight and sound while handling modest torque. The steel shaft ensures reliable power transmission in tight rooms.
** Industrial Machinery **: Suitable for conveyor systems, product packaging equipment, and automated assembly lines, where resistance to chemicals, dust, and dampness is vital. The helical layout reduces vibration, prolonging machinery life expectancy.
** Medical Tools **: Used in imaging devices, surgical robotics, and mixture pumps, where precision and sterilization compatibility are essential. Plastic equipments protect against contamination, while steel shafts preserve alignment precision.
** Robotics and Automation **: Necessary for robotic joints, grippers, and CNC machinery, offering peaceful operation and high torque transmission. The hybrid building and construction equilibriums durability with energy effectiveness.
** Aerospace and Protection **: Made use of in actuators, touchdown equipment systems, and satellite mechanisms, where weight decrease and resistance to extreme temperatures are critical.
** Consumer Electronics **: Integrated right into printers, electronic cameras, and home devices for silent, portable motion control. Plastic equipments minimize operational noise, boosting user experience.
** Renewable Energy **: Applied in solar tracker systems and wind turbine pitch controls, where rust resistance and reliability under variable tons are essential.
Personalization permits tailoring equipment measurements, tooth accounts, and material mixes to meet specific tons, speed, and environmental demands. Benefits include lowered upkeep, longer life span, and optimized performance in space-constrained or harsh settings. By combining plastic’s convenience with steel’s effectiveness, these gears attend to difficulties across markets, delivering affordable, high-performance services.
Company Introduction
Established in 2002, Port of Machinery Co.,ltd. focus on metal research and mining machinery spare parts. 2 factories over an area of 13,300 square meters, based on 100+ sets of equipment, our production capacity reaches 12000 Tons/Year. has passed ISO 9001 quality managment system certification in 2008.
Our mainly products are dragline excavator spare parts,rotary kiln spare parts, large modulus gear (gear shaft), gearbox ect. 40+ patents with over 45 years experience to help focus on improve the service life of spare parts. We belive that more than 80% reason of mechanical parts’ working life depends on hot processing (steel making/forging/casting/welding/heat treatment). Eight material engineers will control the quality from the original resource.
If you are interested, please feel free to contact us.
Payment
L/C, T/T, Western Union, Paypal, Credit Card etc.
Shipment
By sea, by air, by express, as customers request.
5 FAQs of Custom made plastic helical gear with metal shaft
1. **What materials are used in custom plastic helical gears with metal shafts?**
The plastic component is typically made from high-performance engineering plastics like nylon (PA), polyoxymethylene (POM), or acetal, chosen for their wear resistance, low friction, and noise reduction. The metal shaft is commonly stainless steel, aluminum, or carbon steel, providing structural strength and durability. Material selection depends on application requirements such as load capacity, environmental conditions, and thermal stability.
2. **What are the advantages of combining plastic gears with metal shafts?**
This hybrid design merges the benefits of both materials: plastic reduces weight, minimizes noise, and resists corrosion, while the metal shaft enhances torque transmission, ensures precise alignment, and improves load-bearing capacity. It’s ideal for applications requiring smooth operation, durability, and cost efficiency compared to all-metal gears.
3. **Can I customize the dimensions and specifications of the gear and shaft?**
Yes, these components are fully customizable. Parameters like gear module, helix angle, shaft diameter, length, and spline design can be tailored. Engineers can adjust tooth profiles for optimal meshing, balance torque requirements, and ensure compatibility with existing systems. Custom coatings or treatments (e.g., lubrication, hardening) are also available.
4. **What applications are these gears suitable for?**
They are used in automotive systems (steering, transmissions), industrial machinery (conveyors, pumps), medical devices, and robotics. The combination suits moderate to high-load environments requiring quiet operation, corrosion resistance, and longevity. They perform well in humid, chemical-exposed, or temperature-variable settings where traditional metal gears may fail.
5. **What is the typical lead time and minimum order quantity (MOQ)?**
Lead times vary from 2–6 weeks, depending on design complexity and production methods (e.g., injection molding, CNC machining). MOQs start at 100–500 units for standard designs, but smaller batches are possible for prototypes or niche applications. Bulk orders often reduce per-unit costs and accelerate turnaround.
(Custom made plastic helical gear with metal shaft)
REQUEST A QUOTE
RELATED PRODUCTS
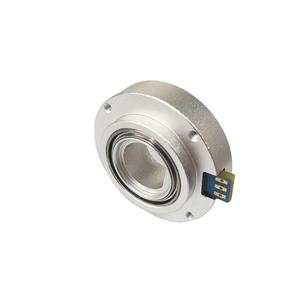
Hot Light weight Eco-Friendly Plating golf putter shaft
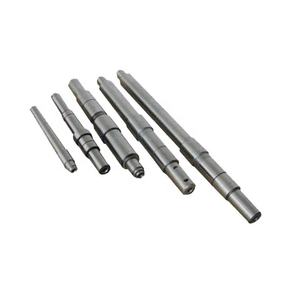
Hardware spare parts turning and milling automatic CNC lathe processing High Precision Crank Shafts Linear Rod Shaft
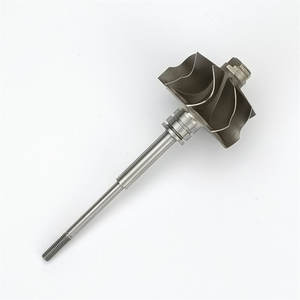
DRIVE SHAFT FLANGE Isuzu Truck Parts 1-37245130-0 Steel Flange
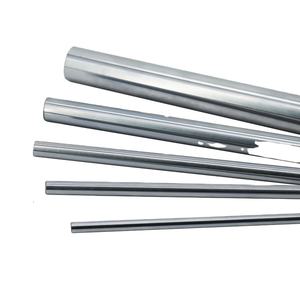
EC16 Insulated Shaft Rotary Encoder
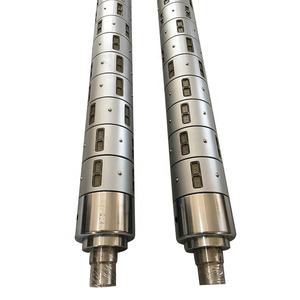
Screw Fasteners Motor shaft 410 420 Stainless Steel Screws Drive shafts For Juicer
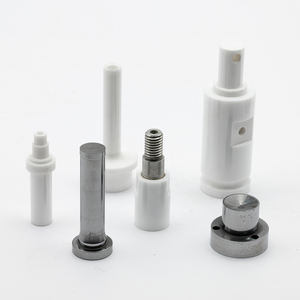