PRODUCT PARAMETERS
Description
Introduction to Insert molding nylon helical gear with iron shaft for machine
Insert molding nylon helical gear with iron shaft for machine are important components in mechanical systems used to support rotating parts (such as gears, pulleys or sprockets) and transmit torque. They play a key role in mechanical equipment by connecting the power source with the working parts to ensure the effective transmission of power.
Characteristic advantages of Insert molding nylon helical gear with iron shaft for machine
High precision: adopting precision machining technology ensures the size and shape accuracy of the shaft and improves the transmission efficiency.
High strength: made of high-quality materials with good tensile, compressive and wear-resistant properties.
Reliability: After strict quality control, it ensures stable operation for a long time.
Versatile design: A variety of specifications and types are available to suit different applications.
Easy maintenance: the structure is designed for easy installation and repair, reducing maintenance costs.
(Insert molding nylon helical gear with iron shaft for machine)
Specification of Insert molding nylon helical gear with iron shaft for machine
The insert-molded nylon helical gear with an iron shaft is developed for high-performance mechanical applications, incorporating toughness, precision, and sound reduction. The gear is produced using engineering-grade nylon (commonly PA6 or PA66) for the helical gear part, providing high tensile toughness, put on resistance, and reduced friction. The iron shaft, typically made from precision-machined carbon steel (e.g., SS400 or S45C), is insert-molded into the nylon gear, ensuring a smooth, durable bond for effective torque transmission. Trick requirements consist of a component range of 1– 4 mm, 15– 60 teeth, and helix angles in between 15 °– 30 ° to enhance smooth meshing and lots distribution. The shaft diameter varies from 8– 40 mm, with custom lengths and keyway/spline choices available. Lots capacity supports continual torque up to 50 Nm and axial/radial loads up to 800 N, relying on size and material quality. Running temperatures range from -40 ° C to 120 ° C, with marginal thermal expansion for secure efficiency. The helical layout reduces noise and resonance contrasted to spur gears, ideal for high-speed machinery. The nylon gear resists rust, chemicals, and moisture, while the iron shaft includes anti-rust layers (zinc, nickel, or black oxide) for severe settings. Applications include commercial equipment, automotive systems, robotics, conveyor systems, and heating and cooling tools. Benefits include lightweight building (30– 50% lighter than all-metal equipments), decreased maintenance due to self-lubricating nylon, and expense performance. Accreditations comply with ISO 9001 for quality assurance, with dimensional precision within ± 0.05 mm and backlash tolerance under 0.1 mm. Customization alternatives consist of tooth profiling, shaft finishes, and resistance modifications. The insert molding process makes certain no loosening or misalignment, boosting durability under cyclic loads. This item is perfect for designers looking for a balance of stamina, quiet procedure, and corrosion resistance in small power transmission systems.
(Insert molding nylon helical gear with iron shaft for machine)
Applications of Insert molding nylon helical gear with iron shaft for machine
Put molding nylon helical equipments with iron shafts are sophisticated mechanical parts designed for high-performance applications across various industries. This manufacturing strategy integrates a durable iron shaft into a nylon helical equipment through a precise molding process, producing a smooth bond that enhances stamina, decreases weight, and enhances functional efficiency. These equipments are suitable for applications needing smooth torque transmission, sound decrease, and resistance to put on, deterioration, and chemicals.
** Industrial Equipment **: These equipments are commonly utilized in conveyor systems, product packaging devices, and automated assembly lines. The helical style ensures peaceful, vibration-free procedure, crucial for maintaining accuracy in high-speed production settings. The iron shaft gives architectural integrity to deal with hefty tons, while the nylon gear teeth minimize rubbing and energy loss.
** Automotive Equipments **: In cars, they are employed in power home window systems, seat insurers, and transmission systems. The combination of nylon and iron offers a light-weight service that endures recurring motion and temperature variations. Their self-lubricating residential or commercial properties minimize maintenance requirements, improving durability in harsh under-hood conditions.
** Medical Devices **: Insert-molded equipments are made use of in analysis equipment, infusion pumps, and surgical tools. The nylon component’s corrosion resistance guarantees compatibility with sanitation procedures, while the helical teeth provide smooth, specific activity control vital for delicate medical applications.
** Agricultural Equipment **: These equipments are indispensable to harvesters, tractors, and irrigation systems, where direct exposure to moisture, dust, and chemicals prevails. The nylon’s resistance to ecological destruction and the iron shaft’s load-bearing capability ensure trustworthy performance sought after outside settings.
** Customer Electronics **: They optimize efficiency in printers, robot vacuum cleaners, and heating and cooling systems by reducing operational sound and boosting power effectiveness. The insert-molded style avoids shaft slippage, ensuring constant efficiency over time.
Key benefits consist of lowered production expenses (through part consolidation), enhanced toughness, and enhanced effectiveness. The nylon equipment dampens vibrations, while the iron shaft makes certain specific positioning and torque transmission. This combination is ideal for applications stabilizing strength, light-weight layout, and resistance to use. Industries take advantage of prolonged element life-spans, lower maintenance prices, and improved system reliability, making these equipments a functional solution for contemporary mechanical challenges.
Company Introduction
Established in 2002, Port of Machinery Co.,ltd. focus on metal research and mining machinery spare parts. 2 factories over an area of 13,300 square meters, based on 100+ sets of equipment, our production capacity reaches 12000 Tons/Year. has passed ISO 9001 quality managment system certification in 2008.
Our mainly products are dragline excavator spare parts,rotary kiln spare parts, large modulus gear (gear shaft), gearbox ect. 40+ patents with over 45 years experience to help focus on improve the service life of spare parts. We belive that more than 80% reason of mechanical parts’ working life depends on hot processing (steel making/forging/casting/welding/heat treatment). Eight material engineers will control the quality from the original resource.
If you are interested, please feel free to contact us.
Payment
L/C, T/T, Western Union, Paypal, Credit Card etc.
Shipment
By sea, by air, by express, as customers request.
5 FAQs of Insert molding nylon helical gear with iron shaft for machine
**What is insert molding, and how is it used for nylon helical gears with iron shafts?**
Insert molding is a manufacturing process where a pre-made component (like an iron shaft) is placed into a mold, and molten nylon is injected around it. For helical gears, this bonds the iron shaft and nylon gear teeth into a single, robust unit. The process ensures precise alignment, reduces assembly steps, and enhances durability by combining metal strength with nylon’s lightweight, low-friction properties.
**Why combine nylon and iron in helical gears?**
Nylon offers noise reduction, corrosion resistance, and self-lubrication, while the iron shaft provides structural rigidity and high torque resistance. This hybrid design balances lightweight efficiency with the strength needed for high-load applications. It’s ideal for machinery requiring smooth, quiet operation without sacrificing performance, such as automotive systems or industrial equipment.
**What temperature ranges can these gears withstand?**
Standard nylon gears handle temperatures up to 220°F (105°C). For higher heat environments (up to 300°F/150°C), heat-stabilized nylon variants or additives can be used. The iron shaft’s thermal conductivity also helps dissipate heat, but prolonged exposure beyond the material’s limits may cause deformation or wear.
**How durable are nylon helical gears with iron shafts under heavy loads?**
The helical design distributes load evenly across gear teeth, reducing stress points. Nylon’s fatigue resistance and the iron shaft’s strength make these gears suitable for medium-to-high torque applications. However, load capacity depends on gear size, nylon grade, and shaft dimensions. Proper alignment and lubrication further extend lifespan in demanding conditions.
**Can these gears be customized for specific machinery?**
Yes. Insert molding allows flexibility in gear dimensions, tooth profiles, and shaft diameters. Customization options include modifying nylon composites (e.g., adding glass fiber for stiffness) or tailoring shaft coatings (e.g., anti-rust treatments). Engineers can optimize gear geometry for noise reduction, efficiency, or torque requirements, ensuring compatibility with diverse industrial applications.
(Insert molding nylon helical gear with iron shaft for machine)
REQUEST A QUOTE
RELATED PRODUCTS
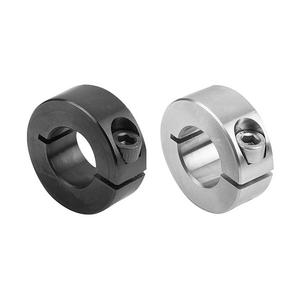
Va Ve Vd End Water Seal Nbr V-type Water Seal Shaft With Mechanical Seal
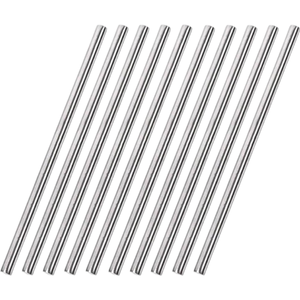
High precision CNC machined stainless steel thread screw spline shaft
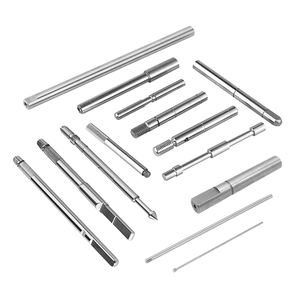
3 inch to 6 inch 3 inch to 8 inch plastic core shaft chuck
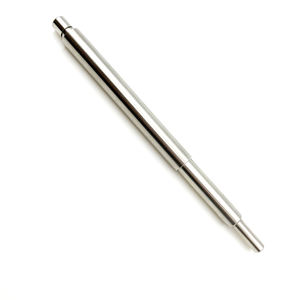
original Konica Minolta Release Shaft /1 (A5AW824300) for Konica Minolta AccurioPress C6085
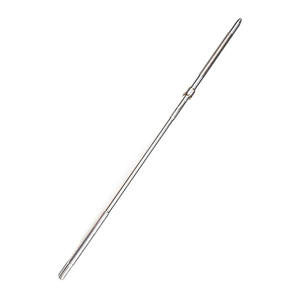
Universal Durable Swing Arm Bushing Middle shaft sleeve back flat fork bushing
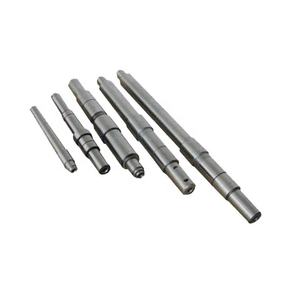